The Perfect Combination of High-Speed Press and Hexagonal Roller Guide Pillar for Precision Terminal Connector Mold
As the era progresses and technology innovates, various applications have increasingly high demands for terminal products, especially for high-frequency and floating connector products. These demands include smaller dimensions, smaller pin pitches, thinner materials, tighter tolerances, minimal burrs, smooth functional surfaces, and stable and safe usage. Apart from high-quality requirements, cost-effectiveness is also essential. However, production and labor costs are continually increasing, posing higher challenges to the manufacturing process of connector terminals, with molds being a crucial aspect.
Traditional connector terminal molds have low precision, requiring frequent adjustments. Ordinary presses have low punching speeds (200-400 SPM), resulting in a daily output of around 400K PCS given this production scenario. This output is insufficient for terminals with large quantities and low unit prices, offering no competitive advantage.
To address these issues, updates are necessary in connector production equipment, mold design, and mold processing to achieve high quality while continuously enhancing production efficiency and reducing manufacturing costs.
With advancing technology, significant improvements have been made in press equipment. Punching speeds have increased from 200 ~ 600 SPM to 200~1000 SPM, and even exceeding 2000 SPM in advanced high-speed presses such as KYORI, BRUDERER, YAMADA, which are widely used in the market. These presses provide a high-efficiency and stable platform for ultra-precision molds for connectors, with slide perpendicularity and parallelism reaching 0.003mm.
Traditional connector terminal molds have low precision, requiring frequent adjustments. Ordinary presses have low punching speeds (200-400 SPM), resulting in a daily output of around 400K PCS given this production scenario. This output is insufficient for terminals with large quantities and low unit prices, offering no competitive advantage.
To address these issues, updates are necessary in connector production equipment, mold design, and mold processing to achieve high quality while continuously enhancing production efficiency and reducing manufacturing costs.
With advancing technology, significant improvements have been made in press equipment. Punching speeds have increased from 200 ~ 600 SPM to 200~1000 SPM, and even exceeding 2000 SPM in advanced high-speed presses such as KYORI, BRUDERER, YAMADA, which are widely used in the market. These presses provide a high-efficiency and stable platform for ultra-precision molds for connectors, with slide perpendicularity and parallelism reaching 0.003mm.

As terminal requirements increase, precision requirements for connector molds also rise. Meanwhile, mold processing equipment has been continuously upgraded from conventional fast wire cutting to slow wire cutting, oil cutting, PG, JG, etc., improving precision from 0.02mm to 0.002mm. These equipment improvements aim to enhance mold precision, lifespan, reduce mold adjustment time, and increase production efficiency.
In the structure of connector molds, the guiding system is crucial, with the internal guiding system (commonly known as "internal guide pillar") being the most critical component. Its importance is akin to a computer's CPU, as the entire mold relies on the internal guide pillar for precise positioning and guidance. When the mold operates, only when the internal guide pillar accurately positions, can other parts be accurately guided into their corresponding positions, forming products with the required shapes and dimensions. If the internal guide pillar cannot position accurately, other parts may cause deviation, resulting in significant deviations in product shape and size, greatly shortening the lifespan of the parts, and even leading to part damage, rendering the mold unusable.
In practical applications, common guide pillars include circular single-pillar, circular cross-roller guide pillar, and hexagonal cross-roller guide pillar. Among them, the hexagonal cross-roller guide pillar is currently the most precise. It offers several advantages:
In the structure of connector molds, the guiding system is crucial, with the internal guiding system (commonly known as "internal guide pillar") being the most critical component. Its importance is akin to a computer's CPU, as the entire mold relies on the internal guide pillar for precise positioning and guidance. When the mold operates, only when the internal guide pillar accurately positions, can other parts be accurately guided into their corresponding positions, forming products with the required shapes and dimensions. If the internal guide pillar cannot position accurately, other parts may cause deviation, resulting in significant deviations in product shape and size, greatly shortening the lifespan of the parts, and even leading to part damage, rendering the mold unusable.
In practical applications, common guide pillars include circular single-pillar, circular cross-roller guide pillar, and hexagonal cross-roller guide pillar. Among them, the hexagonal cross-roller guide pillar is currently the most precise. It offers several advantages:

- Contact between the roller and the guide pillar is a surface contact, unlike the point contact of ball roller guide pillars. The contact area is several times that of ball roller guide pillars, and it possesses rigidity and precision unachievable by ball roller guides.
Figure 3: Precision roller guide pillar vs. precision ball roller guide pillar
- Using rollers can reduce collisions, friction, and vibration during insertion, achieving ultra-high precision linear motion.
- Rollers can distribute pressure, significantly extending the service life of guide pillars.
- High rigidity: From point contact to line contact, by using high-precision wide-width rollers, the rigidity exceeds that of ball rollers by more than 10 times.
- Low vibration: By using high-precision wide-width rollers, while ensuring rigidity, ultra-low preloading can be achieved, thereby realizing ultra-low vibration and smooth rolling.
- High precision: Precision roller guide pillars achieve high rigidity, low vibration, excellent linear motion characteristics, with a repetition precision of more than three times that of ball-type rollers.
Considering the above advantages, using roller guide pillars in ultra-precision molds for connectors can increase mold lifespan, improve mold precision, make guidance more accurate, stabilize mold production, and increase press speeds by 2 to 3 times. With precise guidance and high mold processing accuracy, some connector terminal molds can even produce one output to two or one output to four, combined with advanced high-speed presses, punching speeds can be increased to 900 SPM~1000 SPM. Calculating based on one output to two, daily output can be increased from the original 400K PCS to 2,300K PCS. High-precision connector terminal molds with good punching speed performance can also reduce mold adjustment frequency, increase mold lifespan, and reduce production costs, making them more competitive in the market.

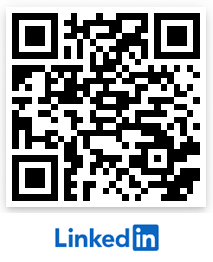
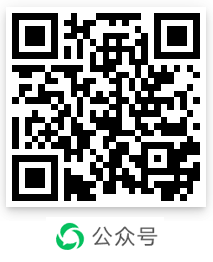