The Function of Floating Connectors Used in Display Screen Products
The increasingly wide application of LED display products has greatly driven their demand growth, especially for small-pitch displays, which account for nearly 50% of the total demand. At the same time, the specification and performance requirements of the connectors used along with this type of application have also heightened. Among them, the stability of the connector that connects the screen light board and the module becomes increasingly important, as it undertakes the role of the transmission of both signal and power between the two parts. Floating connectors have been designed to accommodate for this type of change in design and perfectly meet the demand due to their unique advantages as explained below.
Floating Mechanisms: Well Suitable for Blind-Mate Assembly of Display Products
On one hand, light boards and modules of general products are assembled in the positive direction with the offset tolerance being small and easy to control. On the other hand, those of display products are often assembled blindly with a certain inclination angle. The traditional fixed connectors, providing a more solid, hard connection when facing the offset tolerance of multiple pairs of connectors being used at the same time, make the blind-mating assembly difficult, require more manpower, and easily become damaged. In addition, relying on signal terminal only to provide signal and power transmission requires a structure with more pins, which is not suitable for PCB space design of small-pitch display screens. Therefore, a floating connector with its floating mechanism design is able to absorb tolerances and transmit signal and power together, creating the ideal product to be used in display applications.High Performance for Display Product Application Requirements
Due to its unique structural design, floating connectors can achieve the high performance requirements needed to match the application scenarios of the display screen products, including mechanical, electrical, and environmental performance. Among them, mechanical performance is related to the mating and unmating capabilities; electrical performance includes the requirements for contact and insulation resistance; environmental performance includes temperature, humidity, shock, and impact resistance. In addition, floating connectors can also meet the needs of end users for product miniaturization, functionality, and flexibility. Miniaturization usually means that the three-dimensional size of the connector should be as small as possible. Functionality requires a connector to realize the function of transmitting signal and power at the same time, saving assembly space. While flexibility requires the absorption of welding deviation and assembly deviation.Multiple Pitch and Stacking Heights Provide Flexible and Efficient Connection
Focusing on connector manufacturing for more than 25 years, Greenconn has launched various series of floating board-to-board connectors with a wide variety of different pitch, pin number, and stacking height options (as shown in Figure 1), which can flexibly achieve efficient connections. These connectors have been widely used in display screens and many other applications, and have become very well-reputed.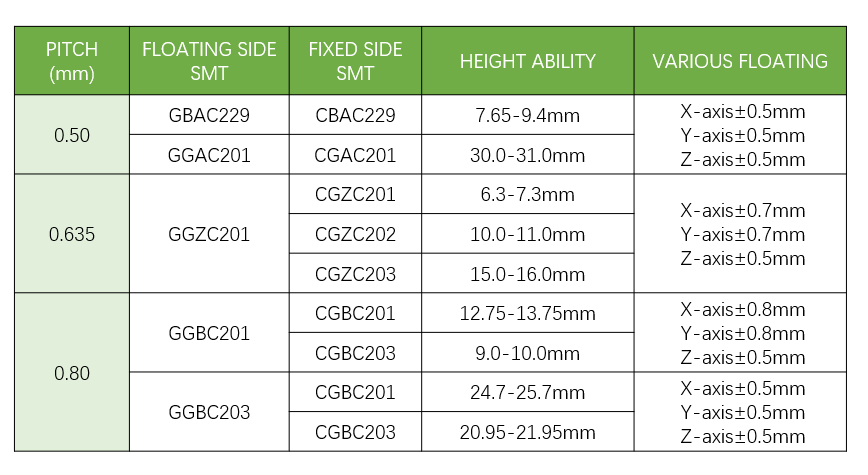
Greenconn’s floating board-to-board connectors adopt the integrated design of a power terminal and signal terminal (3A of power supply and 0.5A of signal transmission), which greatly saves PCB space. The plastic chamfer can absorb a length and width assembly deviation of 0.5mm. The U-shape power and signal terminal also has a superb rebound effect. In addition to allowing for a blind mating assembly, a 10.5° flip-out is designed in the length direction, with no interference at each assembly point. Meanwhile, the gap design at the socket can protect the plastic from being squeezed and broken.
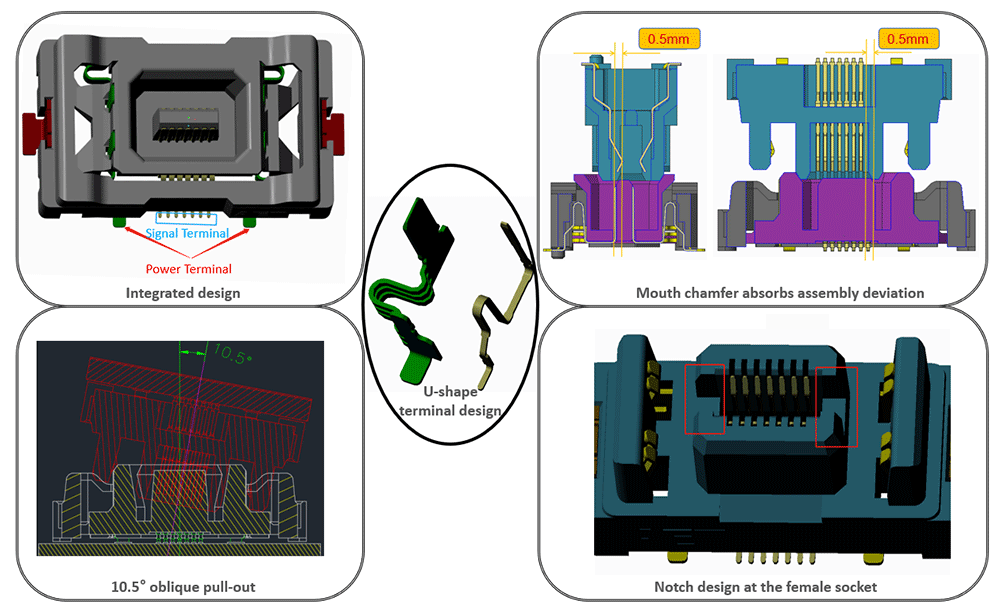
In practical applications, Greenconn can also optimize and adjust all aspects of products according to the terminal application, so as to achieve cost-effective solutions with a high level of functionality.
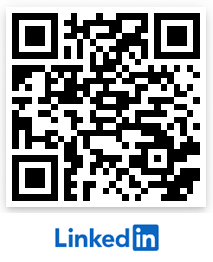
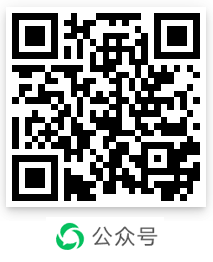