Connector Performance Decline? Quick Diagnosis and Repair Guide

1. Visual Inspection is the Foundation
First, carefully observe the connector from the outside, looking for visible damage, corrosion, burn marks, or contamination. These obvious issues are often the direct cause of performance decline.
2. In-Depth Performance Testing
- Contact Resistance Test: Measure the contact resistance of the connector using professional equipment to determine if there is poor contact.
- Insulation Resistance Test: Evaluate the insulation performance of the connector to ensure there is no insulation degradation, preventing leakage risks.
- Withstanding Voltage Test: Verify whether the connector can withstand the specified voltage level to ensure electrical safety.
- Signal Integrity Test (for high-speed data transmission): Ensure that data transmission is free from interference, maintaining signal quality.
3. Vibration and Environmental Adaptability Evaluation
- Vibration Test: Simulate the vibration conditions of the actual working environment to check if the connector can maintain a stable connection.
- Environmental Factors Check: Analyze the impact of humidity, temperature, chemical corrosion, and other environmental factors on the connector, and take appropriate measures.
4. Detailed Inspection of Mechanical Components
Carefully inspect the mechanical components of the connector, such as latches, screws, and terminals, to confirm there is no damage or wear. The integrity of these components directly affects the stability and durability of the connector.
5. Cleaning and Maintenance are Essential
Once contamination or corrosion is detected, immediately use appropriate cleaning agents and tools to thoroughly remove any contaminants that may affect performance.
6. Replace Parts When Necessary
For damaged parts, such as terminals or seals, replace them promptly to restore the normal function of the connector.
7. Ensure Proper Reassembly
After replacing parts or performing other maintenance, reassemble the connector according to the manufacturer’s specifications to ensure all connections are correct.
8. Software Diagnosis for Troubleshooting
If the connector is used with electronic systems, use diagnostic software to check system logs, which can help identify potential errors or warnings and further locate the problem.
9. Professional Consultation for Complex Issues
For complex or hard-to-diagnose problems, do not hesitate to consult the manufacturer or professional technicians. Their experience and expertise will provide strong support.
10. Record and Analyze to Prevent Recurrence
Keep detailed records of the diagnosis process and repair results, analyze the root cause of the performance decline, and take preventive measures to avoid similar issues in the future.
11. Prepare Backup Plans for Emergencies
For critical applications, it is advisable to prepare backup connectors or systems to enable rapid replacement in emergencies, ensuring business continuity is not affected.
By following these steps, you can quickly diagnose connector performance issues and take appropriate repair measures to restore the normal working condition of the connector.
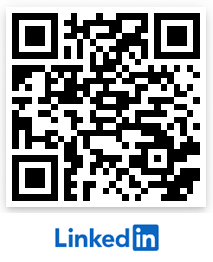
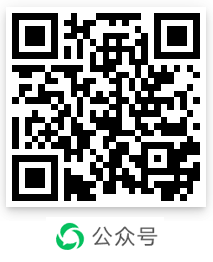